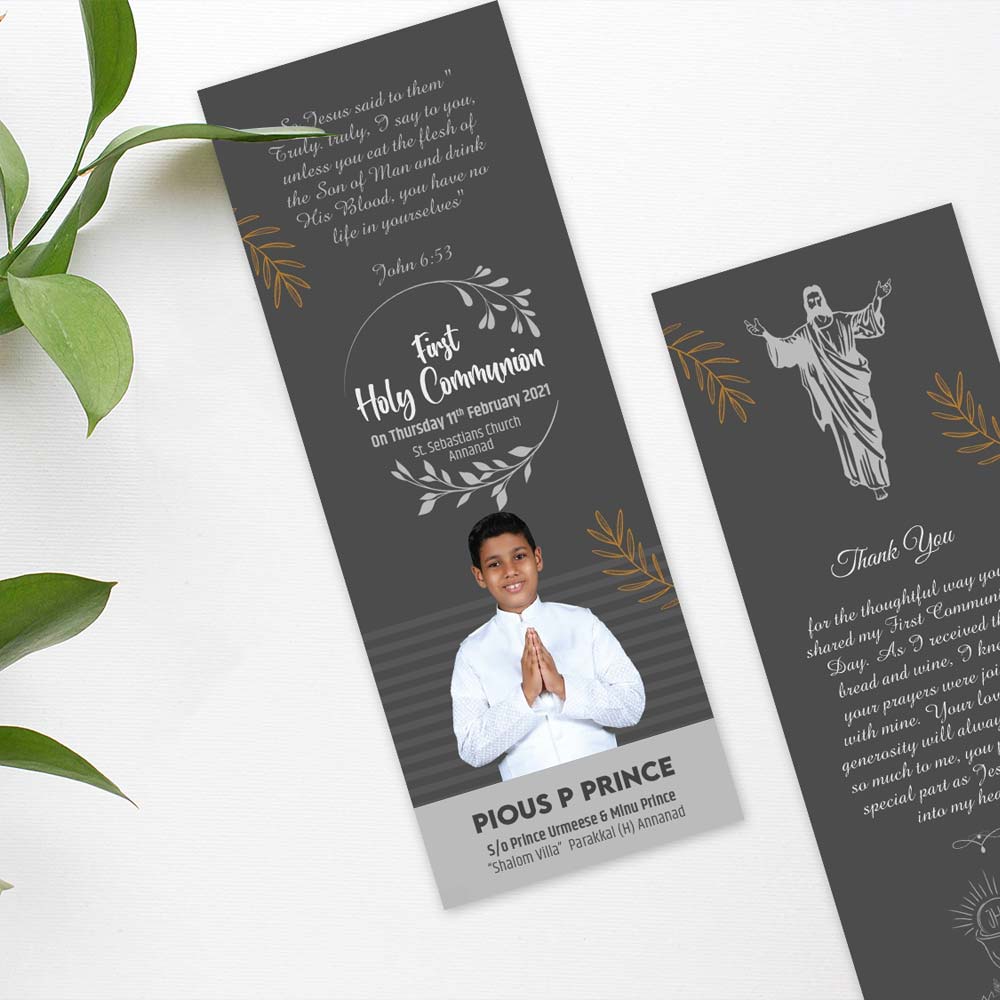
Holy Communion Invitation Cards
Custom Design & Sizes Available
We're a one stop website for sale of designer invitation cards for all occasions. No hassles of visiting crowded markets to purchase invitation cards, you can now choose invitation cards from the convenience of your home and we deliver it at your doorstep.
Custom Designs Available
Optional Lamination & Foiling
Different Materials Available
Due to the unexpected changes in the cost of the raw materials we use in our production process, we request you to contact us and confirm the price


PDF is our preferred format. All font/Text should be Outlined/ Curved while creating/converting to pdf. JPEG provides good quality outcomes if the file is converted under certain specifications. Text and vector images appear less sharp compared to PDF file format.
COLOURS
The working CMYK profile must be U.S. Web Coated (SWOP) v2. All colours in the design must be CMYK only. Do not use RGB and Panton Colours.
SIZE
Design size should be as per final job size (90 x 53mm, 210 x 280mm, 420 x 280mm, etc). All-important matter in the design should be at least 4mm inside from all edges, so that important matter does not come under cutting. Provision for binding margin for jobs like Book wrapper, Bill Books, Receipts, etc. and extra space for Die-cut should be made within the final job size. All the time it is not guaranteed that the artwork will be placed near the Gripper even if it is requested. Design will not be edited by us. Job size should be from our standard product list only if not the price may vary.
BITMAP
All Drop Shadow, Contour, Blend, Bevel effects should be " break apart ", Convert all lens effect, Fountain Fill, Monochrome EPS, OLE object & images to 300 dpi CMYK bitmap.
For Copies more than 1,000 - first placement (up) in the set will not have any issue after printing. For 2-up, 3-up,....n-up the shadow will be shifted while ripping if Bitmap not done for Drop Shadow. This case is applicable for all Special effects.
OVERPRINT FILL
Do not set colours as "Overprint Fill". Overprint is a way of combining colours when dealing with subtractive colour spaces such as CMYK. When you print non-transparent, overlapping colours, the top colour knock outs the area underneath. When used intentionally, overprint represents an additional way to create artwork that is visually interesting and distinctive. However, if overprint is turned on without your realising it, you will probably end up with prints that look significantly different from what you expected when designing them.
We shall not be held responsible for any Overprint setting in your artwork. Kindly do the self-check for any unwanted Overprint setting in your artwork.
COLOUR RATIO
Letters / texts colours must be formed by two colour combinations only.
Preferably do not put heavy patches in the design. Due to this back set-off will appear.
Avoid any Dark colour tint designs and backgrounds in Special Cards (Corporate, Metallic and Textured Cards), you can't expect the same colour output as in normal 300 GSM boards.
Maintain the total colour ratio less than 210% (Cyan+Magenta+Yellow+Black<210%) to avoid lamination issues.
For single-colour saturations, extremely light ink coverage (under 10%) may not even print at all. We recommend your colour choices, even your darkest sections, stay within the 150%-210% range. This area will show a lot of colour flexibility, while preventing the muddied look when colours approach 300% and above.
In order to make your tint/toning effect more obvious, make sure the value between colours are at least 15% of different.
LINES AND BORDERS
Do not set line weight less than 0.25pts. Avoid borders in the artwork, it is difficult to get even borders after cutting.
SOLID BLACK
Standard black uses only black ink (100% K), whereas rich black contains elements of other colours (30% Cyan, 30% Magenta, 30% Yellow) either.
Refer previous tab "Layout & Format"
This will make the black denser onto an image if you want your background not to show through.
Printer will be solely responsible for rejection of job due to design errors or effects. No complaint in this matter will be accepted.
After Designing keep the size of the artwork at 100% in your software or adjust the size of the artwork design in the computer screen as it match the size of the printed job / card. If the Letters are blur even in the computer screen at this percentage, increase the font size in the design for legibility. Letters with the dark background (more than one colour combination outside the letters) must be large enough to avoid penetration of ink from the combination of colours in the dark background.
Standard Papers / Boards will be used for all other paper Medias mentioned in our product list. All papers / boards of different mills will be used as per their availability, hence variation in brightness, pattern / texture and thickness may appear.
CREASING / FOLDING:
The grain in paper comes from how the fibers of the paper are arranged. We try to consider the grain direction within the framework of print production. However, we cannot exclude slight cracking occurring at the fold.
REPEAT JOBS
Colour and printing may not match in repeat jobs.The two main goals in gang run printing are substantial cost savings and pleasant colour matching. Our press operators balance the colours on all jobs so everyone has a 95%-98% colour consistency. Below you can see the results of having all dark cards on a run versus having light cards. The dark cards may darken your card's image slightly whereas the light images may lighten the image. As you will see in the example of the Fitness Centre card below, the skin tone as card card-body as the colour may shift from run to run.
Since the ganging of jobs is an automated process we cannot change the card order for special requests. If colour matching is critical to your order, we do not recommend gang run printing. A custom run of only your order will give our press operators the control needed to match your colours exactly.
In front-back job, if there is same colour on both the sides, print and colour variation will appear.
Digital Print and Offset Print the colours are non-comparable.
Colour variation will appear in dark shades of Grey, Violet, Blue, Green, Brown, and Orange.
Back set-off will appear on back side of the job for designs having heavy patch.
Spot UV and Gold Foil is not preferred to be at the edges of the visiting card. Cutting will damage the UV coat and foil at the edges.
There could be difference of 0.25 to 0.75 mm in the registration of Spot UV.
If there is borders it is difficult to see even borders after cutting.
To speed the printing process we use a machine like this to cut many sheets at the same time. During the process the sheets may shift so it's very common that any border designed too close to the cutting line will look uneven in the printed product.
During the cutting process there is a 1-2mm margin of error (due to characteristics of the stock, pressure placed on the product when being cut, as well as outside factors that may affect the printing process such as weather, humidity etc.), Shree Maruthi Printers does not guarantee 100% center cuts. Please keep this in mind when creating your design.
DIE-CUT
Cutting Edge Tolerance: + - 1mm.
NOTE: Customers are advised to revise artwork when these problems are detected. Shree Maruthi Printers shall not be held liable for any of defect in printing outcome due to artwork sent not correctly prepared as advised.
If the order status is cancelled / pending that particular order will not be taken by us even the Amount is debited from the account initially. In such case customer can wait for 15-20 min and check for any change in the status i.e. Ready to Batch this will happen only if Payment Gateway has authorised the Payment. If the status is still cancelled / pending even after the wait time, customer can place the order again if it is urgent or need to wait till we receive the record of that order from Billdesk (Payment Gateway). This may take 2-4 days for us to receive the record for cancelled / pending orders. If the Record for the Cancelled / pending order is received it will be reversed to the customer bank account or will be added to the wallet as per the customer's convenience.
On the date of Delivery, Parcels will be handed over to the Transporter / Courier after 7 pm from our Coimbatore Office. Due to some unavoidable circumstances and technical reasons rarely delivery time may change. Parcel will be well packed by us. In rare cases there may be delay / mistakes / damage of the parcel from the transporter / courier in delivering the goods. Company will not be responsible for it. Courier can be tracked in the Courier Company Website.
Marginfree Printers reserves right to refuse any order without giving any reason.
Customer errors include incorrect file submission in accordance with our specifications, duplicate orders, customer misunderstandings of Delivery time, slight colour variances within four-colour (CMYK) industry standards for pleasing colour and designs not within stated cutting and folding tolerances.
Marginfree Printers cannot and does not check any submission for spelling, grammar or any other textual errors. The design will be printed as it appears in the file. It is the sole responsibility of the customer to ensure that all materials submitted for printing are formatted correctly and free of spelling or grammatical errors.
Marginfree Printers does not recommend designs with borders due to the nature of our cutting. We cannot guarantee the bordered design will be perfectly centered after cut.
No compensation is offered for any of the above listed customer errors or for the below items:
- Blank Design
- Asymmetric Borders
- Incorrect card / job orientation
- Wrong Crop marks
- Folding out of spec
- Hard to read
- Mini image
- Missing logo
- No text
- Colours out of the CMYK colour
- Text or important images out of the safe zone
- Texts not Curved
- Bitmapping the Special effects
- Pixelation
- Visible template lines / Die lines
- Contents out of safe zone in die-cut
Apart from these things, customer must take care of all other technical aspects in the design for flawless orders.